LEAN SIX SIGMA CHAMPION
Creating Valuable Human Capital to drive Lean Six Sigma through Lean Six Sigma Champion training
The Lean Six Sigma (LSS) Champion training is especially for Leaders and Managers to learn and understand the DMAIC problem solving approach. It also provides training on other skills that Leaders and Managers need to lead change in their organization. These skills include selection of improvement projects, employee coaching skills, Go See skills and Daily Management huddles.
This is a 2 day class comprising the following modules:
1. Setting the Stage - class objectives, conduct of class, expectations
2. Introducing Lean Six Sigma - benefits and origins of Lean and Six Sigma
3. Change Management - Key elements of managing change
4. LSS Leadership - Changing the way leaders work
5. DMAIC and Define Phase - the DMAIC framework and considerations for Defining the Project Charter and listening to the Voice of the Customer
6. Measure Phase (Part 1- Process Perspective) - Gathering information about the process, mapping the value stream
7. Measure Phase (Part 2 - Data Perspective) - Getting the baseline data and measuring 'data that counts'
8. Analyse Phase (Part 1 - Process Perspective) - Root-cause analysis using lean tools
9. Analyse Phase (part 2 - Data Perspective) - Finding root-causes through data analysis
10. Improve Phase - Developing the counter-measures
11. Go to Gemba Skills - Know how to go to gemba in the correct way
12. Control Phase - ensuring that the improved performance is sustain, planning for and responding to process performance changes
13. Roles in LSS - Knowing the roles of the various personnel in a LSS deployment
14. Wrap Up and Next Steps - leadership discussion on the appropriate next steps to go forward
What is a Lean Six Sigma Champion?
A lean six sigma champion is a person who is an operations or business specialist who has attained substantial practical experience in the many facets of lean management, six sigma, process improvement, and the many lean six sigma tools & techniques. He/she tyoically possesses problem solving skills in different areas of a business. He needs to have leadership skills and is able to motivate employees to make improvements on a continuous basis to achieve team and organizational goals.
Deploying a Lean Six Sigma Champion
One of the vital ingredients of having a successful lean program is to have effective Lean Six Sigma Champions. Lean Six Sigma Champions are selected carefully on a pull basis rather than push. In fact organizations who have a thriving lean program are often driven internally by management champions. Lead Six Sigma Champions lead the way. They spot improvement opportunities. They motivate employees to do something about the issues they face. They act to remove obstacles that are in the way to success.
Contact
Thank you for your interest in our services. We will be happy to answer any questions you may have. Feel free to contact us:
Eagles Wings Consulting Pte Ltd
Email: robert@eagles-wings.info
Tel: 9735 1136
Why Eagles Wings Consulting?
* Lean, Six Sigma, Agile & Service Design
* Leadership and ground level experience
* Operating since 2004
* Based in Singapore
* Training, Consulting & Coaching
* Clients from many industries including Health-Care, MRO, IT, Education, Government, Oil & Gas, Manufacturing, Finance, Telecoms and many others

The Kata of Karate
The word 'karate' comes from the word 'kata'. Kata can be thought of as a practiced routine set of actions that one has internalised, which become a habit, almost an unconscious way of doing things. Toyota kata is hence an internalised routine method of learning from trials, making adjustments that are necessary, and implementing the next improvement in moving from the current condition towards a target condition. It is the real Plan Do Check Act (PDCA) actions that allow us to continuously improve.
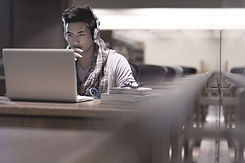
Lean IT: What is it?
It is actually, quite a large subject. I will endeavour to describe what Lean IT is all about in several articles over the next few months. I will begin by referring to the many tools & techniques of Lean. In Lean (whether Lean IT or Lean used in other functions/industries) there are many tools and techniques. Broadly these tools & technqiues can be categorized into 5 main groups, for Problem Solving, Improving Process Flow, Direction Management, Daily Management and Building Continuous Improvement Culture