LEAN A3 PROBLEM SOLVING
A step by step Lean problem solving approach to resolve issues in your value streams

Lean A3 Problem Solving - Course Description
This course is especially designed to develop skills and knowledge on how to solve problems and provide an opportunity to ‘learn by doing’ by working on actual problems found at the participants work-place:
1) This activity-based training takes participants in a step by step method through the A3 thinking process (a series of divergent-convergent steps to solve problems). It makes use of numerous activities and 3 simulation runs to tightly couple and integrate the knowledge and learning of key lean tools with the A3 problem solving process. Learn by doing is a key feature of this training where participants will learn the A3 problem solving process and several key lean tools and techniques through the practical exercises, simulation runs and working on actual problems from the participants work-place.
2) To make best use of time the problems each team will work on will need to be pre-identified before the class. A project charter is prepared by each team and submitted before the class (optional).
The course objectives are as follows:
· Learn the concepts, principles and benefits of Lean Management
· Acquire skills on key Lean tools and techniques
· Learn the Lean A3 problem-solving approach to solve problems at your work-place
· Hands-on application of these skills to resolve actual problems at your work-place
· Learn through hands-on practice, activities, demos and simulations
Course Content:
Module 1 – Setting the Stage
· Leadership Case for Change
· Where did Lean come from?
· TIMWOOD-I Wastes
· Post Course Expectations
Module 2 – Specifying Value
· Principles of Lean
· What is A3 Thinking?
· SMART Goals
· SIPOC Diagram
· Stakeholder Management
Module 3 – Identifying the Value Stream
· Value Streams
· Gemba Walk
· Gemba Walk Table
· Simulation Round 1 + De-brief
· Developing Value Stream Maps
Module 4 – Improve the Flow & Introduce Pull (Part 1)
· Root-Cause Analysis
o Fishbone Analysis
o The 5 WHYS
Module 5 – Improve the Flow & Introduce Pull (Part 2)
· Eliminate Obvious Waste
· Impact of Batch Size
· Workload Balancing
· Applying 5S
· Potential Counter-Measures
· PDCA
· Simulation Round 2 + De-brief
Module 6 – Improve the Flow and Introduce Pull (Part 3)
· Spaghetti Diagram
· Load Levelling
· Mistake Proofing
· Sustaining the Gains (Lean SOP & VM)
Module 7 – Pursuing Perfection
· Manage & Communicate visually
· Visual Management and Huddles
· See, Know, Act & Learn Together
· Simulation Round 3 + De-brief
· Elements of Standard Work
· Where to begin building Standard Work?
Module 8 – What are the Next Steps
· Post Course Expectations
· Roles & Responsibilities
· Next Steps
· Closing
Contact
Thank you for your interest in our services. We will be happy to answer any questions you may have. Feel free to contact us:
Eagles Wings Consulting Pte Ltd
Email: robert@eagles-wings.info
Tel: 9735 1136
Why Eagles Wings Consulting?
* Lean, Six Sigma, Agile & Service Design
* Leadership and ground level experience
* Operating since 2004
* Based in Singapore
* Training, Consulting & Coaching
* Clients from many industries including Health-Care, MRO, IT, Education, Government, Oil & Gas, Manufacturing, Finance, Telecoms and many others

The Kata of Karate
The word 'karate' comes from the word 'kata'. Kata can be thought of as a practiced routine set of actions that one has internalised, which become a habit, almost an unconscious way of doing things. Toyota kata is hence an internalised routine method of learning from trials, making adjustments that are necessary, and implementing the next improvement in moving from the current condition towards a target condition. It is the real Plan Do Check Act (PDCA) actions that allow us to continuously improve.
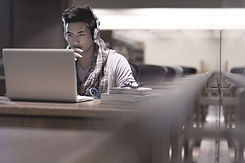
Lean IT: What is it?
It is actually, quite a large subject. I will endeavour to describe what Lean IT is all about in several articles over the next few months. I will begin by referring to the many tools & techniques of Lean. In Lean (whether Lean IT or Lean used in other functions/industries) there are many tools and techniques. Broadly these tools & technqiues can be categorized into 5 main groups, for Problem Solving, Improving Process Flow, Direction Management, Daily Management and Building Continuous Improvement Culture